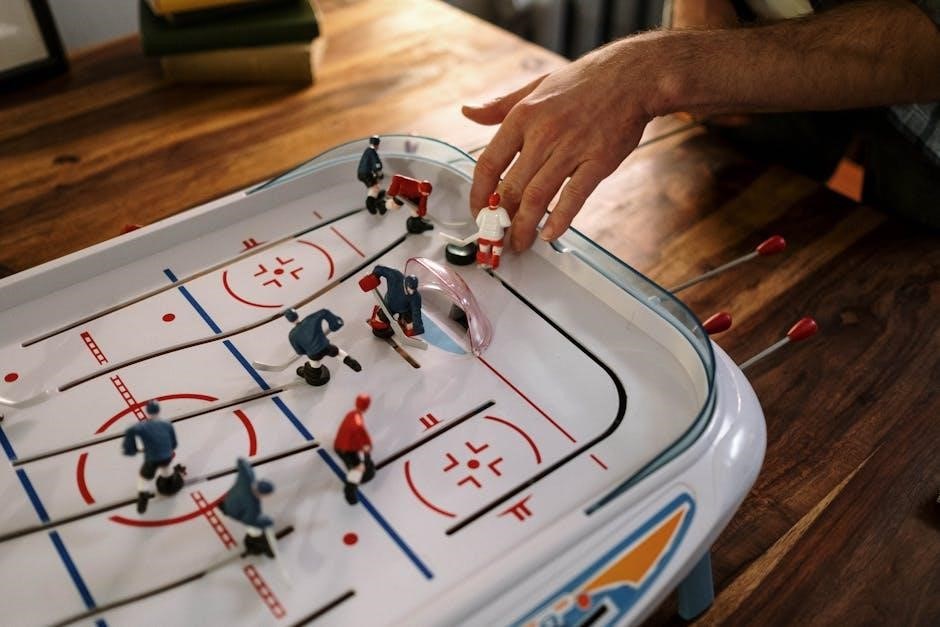
Understanding the Importance of Reliable Ice Supply
A reliable ice supply is crucial for many businesses‚ particularly those in the food and beverage industry‚ as it directly impacts their operations and customer satisfaction. The absence of ice can lead to significant losses and damage to a company’s reputation. With an Ice-O-Matic machine‚ entrepreneurs can ensure a consistent and steady ice supply‚ which is essential for keeping drinks cold and food fresh. The Internet provides various resources and guides on how to maintain and troubleshoot these machines‚ emphasizing the importance of a reliable ice supply. By understanding the significance of a steady ice supply‚ business owners can take proactive steps to prevent disruptions and maintain their operations smoothly. This knowledge is vital for any entrepreneur who relies on ice to run their business‚ and it can be found in various online resources and troubleshooting manuals‚ including those related to Ice-O-Matic machines and their maintenance.
Common Issues with Ice-O-Matic Machines
Flashing Lights and Error Codes
To troubleshoot Ice-O-Matic machines‚ it’s essential to understand the meaning of flashing lights and error codes. These signals indicate specific issues‚ such as problems with the water supply‚ freezing‚ or dispensing. By deciphering these codes‚ users can identify the root cause of the problem and take corrective action. The Ice-O-Matic CIM error light diagnostics guide provides a comprehensive list of error codes and their corresponding solutions. This guide is a valuable resource for users‚ as it enables them to resolve issues quickly and efficiently‚ minimizing downtime and ensuring optimal performance. With the help of this guide‚ users can diagnose and fix problems‚ such as a faulty water valve or a malfunctioning thermostat‚ and get their Ice-O-Matic machine up and running in no time. By following the step-by-step instructions‚ users can troubleshoot and repair their machine‚ saving time and money. The guide is easy to use and understand‚ making it an indispensable tool for anyone who owns an Ice-O-Matic machine.
Refrigerator Ice Maker Troubleshooting
Refrigerator ice maker troubleshooting is a crucial aspect of maintaining a reliable ice supply. The process involves identifying and resolving issues with the ice maker‚ such as dripping or no ice production. According to online resources‚ a common problem with refrigerator ice makers is the formation of ice blocks or frozen water in the dispenser. To troubleshoot this issue‚ users can check the water supply lines‚ ice maker settings‚ and the dispenser itself. The Ice-O-Matic troubleshooting manual provides guidance on how to diagnose and fix these problems; By following the manual’s instructions‚ users can resolve issues with their refrigerator ice maker and ensure a steady supply of ice. The manual also covers topics such as ice maker installation‚ maintenance‚ and repair‚ making it a valuable resource for anyone who owns a refrigerator with an ice maker. With the help of this manual‚ users can troubleshoot and fix problems quickly and efficiently.
Diagnosing the Problem
Checking the Power Supply and Settings
Identifying the Cause of Warm Commercial Ice Makers
Warm commercial ice makers can be a significant issue‚ and identifying the cause is crucial to resolving the problem. The first step is to check the machine’s condenser coils‚ as dirty or clogged coils can cause the machine to produce warm ice. Next‚ inspect the refrigerant lines for any signs of damage or leaks‚ as this can also affect the machine’s ability to produce cold ice. Additionally‚ check the machine’s temperature settings and ensure they are set correctly. It is also important to check the machine’s water supply lines and ensure they are not clogged or restricted‚ as this can cause the machine to produce warm ice. By following these steps‚ you can quickly identify the cause of the issue and take corrective action to resolve it. Using online resources‚ such as troubleshooting guides and repair manuals‚ can also provide more detailed information and guidance on identifying and resolving issues with warm commercial ice makers. Regular maintenance can also help prevent issues.
Ice-O-Matic Commercial Ice Machines
Ice-O-Matic offers reliable commercial ice machines with simple designs and easy-to-use interfaces always available worldwide in various models.
Features and Benefits of Cubers‚ Flakers‚ and Pearl Ice Machines
Ice-O-Matic’s cubers‚ flakers‚ and pearl ice machines are designed to provide high-quality ice for various applications‚ including restaurants‚ bars‚ and hotels. The cubers produce large‚ clear ice cubes that are perfect for drinks and displays. The flakers produce soft‚ fluffy ice that is ideal for cooling food and drinks quickly. The pearl ice machines produce small‚ soft ice pellets that are perfect for cooling drinks and food. All of these machines are designed to be energy-efficient and easy to use‚ with simple interfaces and automatic cleaning systems. They also feature advanced technology‚ such as sensors and monitoring systems‚ to ensure optimal performance and minimize downtime. Additionally‚ Ice-O-Matic’s machines are built with durability and reliability in mind‚ with heavy-duty construction and high-quality components. Overall‚ Ice-O-Matic’s cubers‚ flakers‚ and pearl ice machines offer a range of features and benefits that make them ideal for businesses that need high-quality ice. With their advanced technology and durable construction‚ they are a great choice for any business.
Troubleshooting Guides and Resources
Using the CIM Error Light Diagnostics Guide
The CIM error light diagnostics guide is a valuable resource for troubleshooting Ice-O-Matic machines‚ providing step-by-step instructions and diagrams to help identify and resolve issues quickly and efficiently. By following the guide‚ users can determine the cause of the error light and take corrective action to get their machine up and running again. The guide covers a range of topics‚ including error code definitions‚ troubleshooting procedures‚ and repair techniques. With the CIM error light diagnostics guide‚ users can save time and money by resolving issues themselves‚ rather than calling in a service technician. The guide is available online and can be accessed using a computer or mobile device‚ making it easy to use and convenient to access. Additionally‚ the guide is regularly updated to reflect the latest changes and improvements to Ice-O-Matic machines‚ ensuring that users have the most accurate and effective troubleshooting information available.
Accessing the Diagnostic Panel on Elevation Series Machines
To access the diagnostic panel on Elevation series machines‚ users must first locate the faceplate above the ice bin. The diagnostic panel is hidden behind this faceplate and can be accessed by loosening the two Phillips head screws at the base of the faceplate. Once the screws are removed‚ the faceplate can be lifted up and off‚ exposing the diagnostic panel. The panel features two buttons that must be pressed simultaneously to activate the diagnostic mode. The buttons will turn green and yellow when the diagnostic mode is activated‚ indicating that the machine is ready for troubleshooting. The diagnostic panel provides valuable information about the machine’s operating status and error codes‚ allowing users to quickly identify and resolve issues. By following these steps‚ users can easily access the diagnostic panel and begin troubleshooting their Elevation series machine. The process is relatively simple and can be completed in just a few minutes.